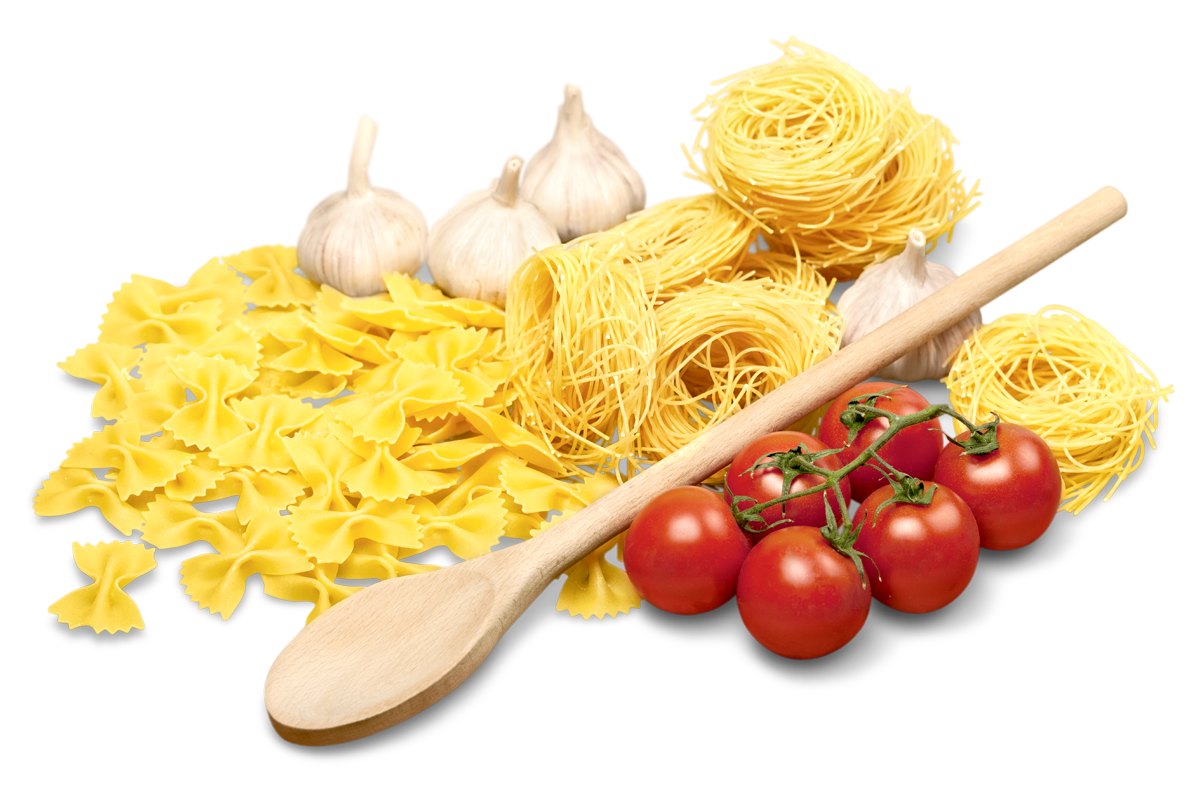
A multifaceted sector
A multifaceted sector
The Food & Beverage sector is vast and includes both the production of food and beverages and therefore the processing of raw materials, as well as quality control, packaging and distribution of products (from large retailers, restaurants, fast-food chains and home delivery).
Eating behaviour is becoming more and more differentiated, constantly and frantically changing. In fact, while there is a growth in the consumption of pre-packaged food, characterised by ease of storage, preparation and eating, there is also a growing search for selected food and food safety. Customers today are extremely attentive and critical in assessing product quality and transparency, they are looking for a more balanced diet, and/or in some cases vegetarian or vegan, they pay attention to product distribution and packaging and are sensitive to eco-sustainability.
How does it respond to changes?
How does it respond to changes?
- Flexibility: all these aspects require the Food & Beverage sector to adopt a more efficient and flexible approach throughout the supply chain.
- Efficiency: electricity consumption for processing, production, filling and packaging systems is one of the most significant items of expenditure for food and beverage companies, as these processes operate continuously, 24/7.
- Reliability: avoiding production downtime or at least reducing start-up time or reaction to faults during operation is key to avoiding or reducing associated costs.
- Connectivity: Both local and remote control systems must be introduced to monitor the correct operation of production processes at any time and from any location to ensure high standards of safety, reliability and traceability.
What needs conditioning?
What needs conditioning?
In the food and beverage industry there are complex automation systems, robots and modular, flexible systems (e.g. conveyor belts for glass and plastic bottles…) that require electrical components to carry out production, processing and packaging tasks. These need to be cooled in order to keep the working temperature within certain limits by protecting them from excessive heat, as well as from contaminants in the environment, while meeting strict hygiene standards.
But not only that, a switch cabinet can be provided at the edge of the production line, for example to cool servers for managing production or logistics data, which individually have low thermal loads. Control cabinets not only require cooling of the internal components for correct and efficient operation, but also high reliability, efficiency, flexibility and connectivity, and are fully part of Industry 4.0 and edge computing systems.
Perfect products for this application
Perfect products for this application
Contact us
Contact us
For any information do not hesitate to write to us, we are at your disposal!